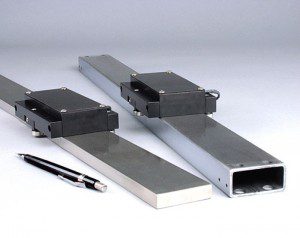
Linear motors come in different mechanical and electromechanical arrangements to satisfy the requirements of different applications. For example, brushless linear motors (capable of forces to 2,600 N or more) work well in heavy robotics or material-handing applications. Linear ac-induction motors output 2,000 N to satisfy heavy-conveyor parameters. In contrast, iron-core brushless linear motors deliver a whopping 15,000 N or more to satisfy the most grueling machine-tool tasks.
But the type of linear motor of focus here are linear stepper motors. True linear stepper motors (and not threaded-rod actuators driven by rotary stepper motors) come in two subtypes that output forces to 250 N—suitable for small robotics and part-transfer motors. For more on this, read:
The two subtypes—variable-reluctance and hybrid—operate much like the equivalent rotary versions.
Variable-reluctance linear stepper motors
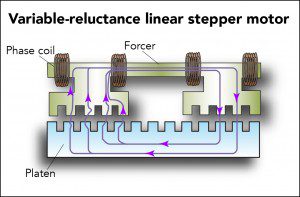
Variable-reluctance linear steppers usually run under three-phase closed-loop control. In short, a forcer with laminated magnetic steel stacks and coils engages a platen when a drive energizes the coils with pulse trains. Each branch (or phase) has one or more teeth; coils wind between the teeth. With no permanent magnets in the setup, the sole input is current.
Variable-reluctance linear stepper motors are an older technology than hybrid motors. Like rotary variable-reluctance stepper motors, variable-reluctance linear steppers can be noisy and are usually only run in full-step mode. But the motors have their own benefits:
- Their platen-forcer electromagnetic coupling minimizes core losses.
- They exhibit less torque drop at higher speeds.
- They are less costly than hybrid linear steppers.
Hybrid linear stepper motors
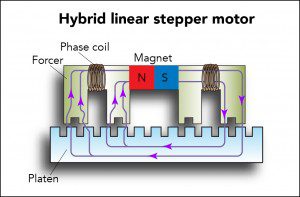
Hybrid linear stepper motors have a carriage-like moving piece (which manufacturers call the forcer) and a stationary track (which manufacturers call the platen). The platen is like that in a variable-reluctance linear stepper. The forcer has permanent magnets, phase coils around magnetic U-shaped stacks, and a magnetic yoke. Each stack has two tooth bodies acting as forcer poles. Coils wind between the teeth. Each tooth body can have one or more teeth. A small gap separates forcer and platen.
Hybrid linear stepper motors have a high detent torque and can operate at high speeds. They drive linear axes in automation, computer peripherals, and robots because they’re accurate and accelerate rapidly. They’re also mechanically simple and reliable—usually with low inertia as well. Hybrid linear steppers usually run under two-phase open-loop control. Their main drawback compared to other types is a higher price point.
For more information, read:
Industrial-Electronics.com: Linear Electric Motors
H2W Technologies: Single-axis linear stepper motors
U.S. patent for variable-reluctance linear stepper motor
HIS Engineering 360: Chapter 3: AC and DC Motors – Servomotors: Linear Motors
Anaheim Automation: Stepper Actuator Guide
Motion Control Tips: Linear Stepper Motors from H2W Technologies
Leave a Reply
You must be logged in to post a comment.