One family of motor drives — tiny ultra-high-current Gold Bee drives from Elmo Motion Control — recently passed highly accelerated life testing (HALT) for accelerated temperatures, electrical cycles, thermal shocks and vibrations.
The tests show that the small servo drive successfully withstands temperatures from -75° to +110° C and easily endures mechanical vibrations exceeding 30 grms.
Gold Bee drives withstood a 48-hour test of exposure to these extreme conditions with zero failures.
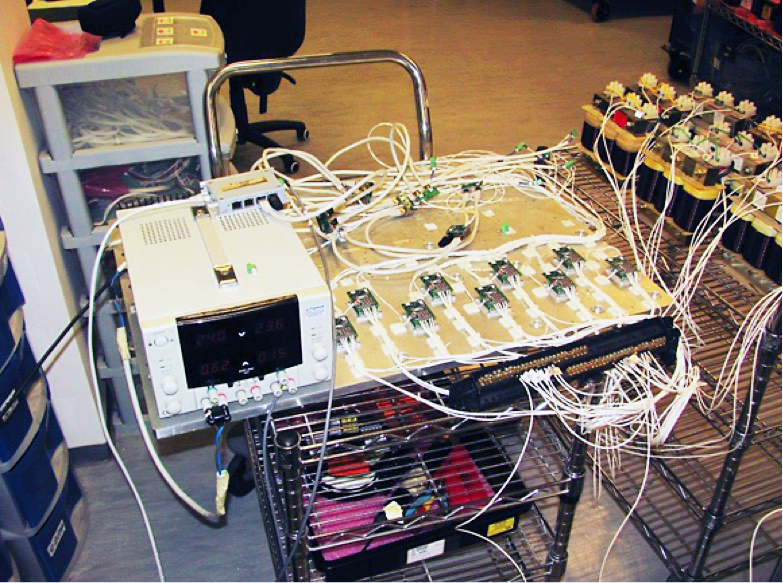
More specifically, a batch of nano-sized Gold Bee G-BEE25/100 servo drives (ones rated for 25-A and 100-V operation) endured HALT that far exceeded the drives’ specified design limits. A testing chamber exposed the drives to -75° C (with an STD of -40° C) and then heated the drives to +110° C (with an STD of 70°C). Then the chamber vibrated the drives to over 30 grms (with an STD = 12 grms) and exposed the drives to cycles from -75° to +110° C at 40° per minute.
More about HALT verification
Highly accelerated life testing (HALT) is a verification process to ensure that a product is reliable enough to withstand a set suite of environmental conditions. Manufacturers perform these tests during the design process — preferably in the pilot pre-production phase — to uncover product weaknesses (if any) prior to design completion and production. The HALT philosophy is that a chain is only as strong as its weakest link … and that tests can discover and correct a product’s weak link or links.
More specifically, HALT subjects products to operate at environmental conditions well beyond its specified and design limits with:
- Accelerated temperature tests
- Electrical cycling tests
- Thermal shock tests
- Vibration tests
By revealing weak-link failures during HALT and then correcting them, manufacturers can establish and then improve product reliability. Taking it a step further, sometimes manufacturers make additional use of extended HALT results to predict a product’s mean time before failure (MTBF).
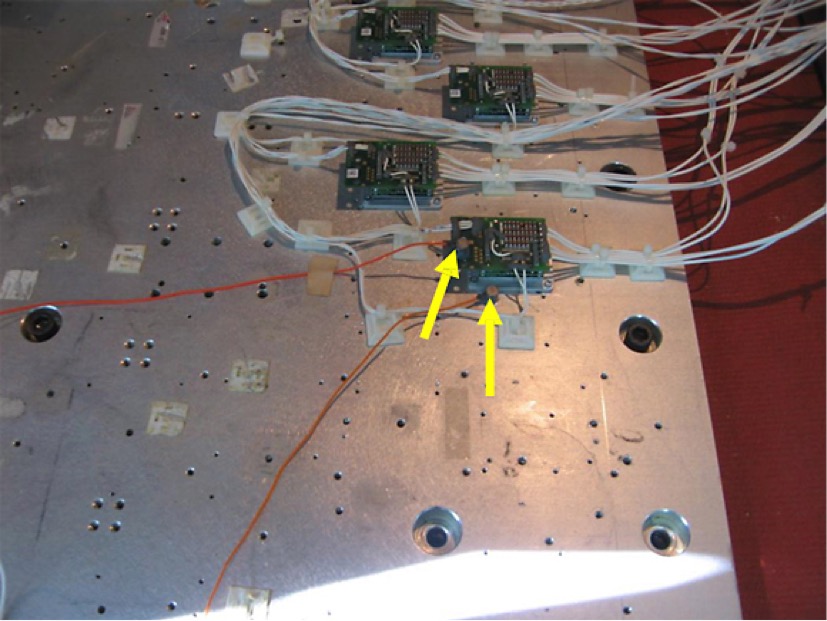
Analysis for this is more complex, requiring considerable more testing and measurements during the HALT process. Note that Elmo plans to publish the results of HALT MTBF for the G-BEE servo drive when analysis of the collected data is done.
HALT and the sources of failures
A typical mistake in electromechanical design analysis is to look for component wear and fatigue due to exposure to extreme environmental conditions. The truth is that electronic-component wear failures are rare and have a negligible effect on overall unreliability. In fact, most electronic malfunctions — those from a motor drive, for example — occur during the initial operating months and result from an inadequate design or a flawed production … both of which HALT detects.
HALT conditions are so extreme that test operators expect the product to eventually break; a successful HALT test is one in which the product fails as the designer expects under the expected conditions of the product design. That lets the manufacturer find failure points for each critical subcomponent and then build a better product iteration.

So because all of Elmo’s G-BEE25/100 drives passed HALT with no failures, does it mean OEMs can install them in applications subject to -55° even though the specification allows only -40° C? Elmo’s engineers give an emphatic no. The manufacturer designed the drives to operate down to -40°C; the fact that it withstands -75° only demonstrates a safety margin. To be clear, operating at ambient temperature lower than -40° C isn’t guaranteed. Designers should contact the manufacturers’ application engineers for help with any machine build that must withstand the drives’ STD operating ratings.
For more information, visit Elmo’s page on the Gold Bee; a full report on HALT; and information on the Gold Bee MTBF (requires registration).
Leave a Reply
You must be logged in to post a comment.