Traditional electromagnetic servo and stepper motors experience electrical and mechanical losses, which result in heat generation and can limit their performance. Piezo motors also experience losses and heat generation, but since they operate via the piezoelectric effect and have no mechanical parts, their performance is affected by different factors.
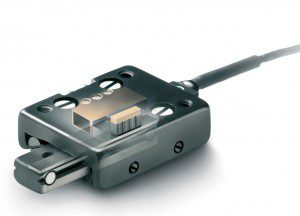
Image credit: MICROMO
Due to their low conductivity and high capacity for heat, piezoceramic materials have a high thermal inertia. This means that it takes them a long time to heat up or to cool down. As a result, a piezo motor won’t experience significant heating when operated intermittently at short-term, high-power conditions. But when the short, high-power operation occurs regularly, the average power (and thus, heat generated) will increase and should be evaluated during design and selection.
The amount of power converted to heat during operation can be calculated as:
Where:
P = power converted to heat (W)
tan δ = dielectric dissipation factor
f = operating frequency (Hz)
C = capacitance of the piezo material (F)
Up-p = peak-to-peak drive voltage (V)
The dielectric dissipation factor is a specification of the dielectric losses inherent in the piezo material. Very little heat is generated during static (holding) operation, but when the voltage is applied at high frequency, heat generated inside the piezo material is proportional to the dissipation factor.
In general, under low-amplitude, low-frequency operation, 1 to 2% of the power through the actuator will be converted to heat. When the actuator is operated at high amplitude, high-frequency conditions, 8 to 12% of the power can be converted to heat, and provisions for cooling may be necessary. Of course, heat conduction to adjacent structures, convection via air, oil, or other fluids, and radiation (in the case of vacuum environments) also have to be considered. The best approach to ensure the motor doesn’t experience overheating is to monitor its heat with a temperature sensor and to run thermal simulations that take into account the motor, adjacent structures, and environmental factors.
Piezo motors do have several benefits over traditional motors when it comes to heat generation. First, they don’t experience the back-and-forth settling motion (commonly referred to as “dithering”) and resulting heat generation that are characteristic of servo motors. Next, piezo motors are able to produce relatively high holding forces without generating heat. And unlike traditional motors, which experience a decrease in efficiency (more power converted to heat) as they get smaller, piezo motors have nearly constant efficiency, regardless of their size.
Feature image credit: Noliac
Leave a Reply
You must be logged in to post a comment.