Updated November 2018 || Common where efficiency (or accuracy) are objectives are synchronous or high-torque drive belts. Applications from consumer-grade home printers to heavy industrial conveyors use these synchronous belts, because unlike V belts with trapezoidal cross-sections, they don’t slip.

Motion applications often need customized belts and sprockets in urethane, double-sided, mini-pitch, and made-to-order (MTO) versions. Double-sided belts have covered teeth to transfer up to 100% of maximum-rated load from one or both belt sides. These come in trapezoidal timing configurations and HTD curvilinear tooth profiles. Some run to 14,000 rpm with speed ratios to 10:1, which is enough to replace gearsets in some cases.
Double-sided belts also excel as serpentine drives in riding mowers with counter-rotating blades, printing presses, and textile machines. Urethane belts maximize motion transfer, especially when incorporating polyester or aramid tensile members. Their tooth profile is a miniature version of belt with standard 40° angle teeth. Speed ratios reach 8:1 and torque output is to a couple lb-in. These belts excel on positioning axes, thanks to their low torque and minimal backlash — especially in printers and copiers that need clean operation.
Long belting (usually with L or H trapezoidal tooth or HTD profiles) can exceed 500 feet in some cases. They work for power transmission and axis synchronization — doing double duty as conveyors in many cases. Such belts complete with rack-and-pinion sets in machine tools and X-ray equipment as a viable drive for linear strokes. One caveat: These belts spliced transmit a quarter less horsepower than a comparable endless belt.

MTO belts are mostly trapezoidal and HTD. Those for applications involving the assembly or transport of electronics or explosive substances include a body and tooth-facing fabric made of conductive material such as carbon to prevent static discharge. In contrast, belts for power tools and appliances are often made of non-conductive materials that insulate internal components. Belts that run in harsh environments incorporate oil-resistant and temperature-resistant compounds.

Elsewhere, tensile members of aramid withstand shock loads, and steel members help belts maintain positioning accuracy. Engineers can even customize the twist of members to alternate or go one way to satisfy tracking requirements. Another option is thick or backed belts to convey or grip objects in tandem with mating belt drives. Backings can also extend belt life and address vibration.
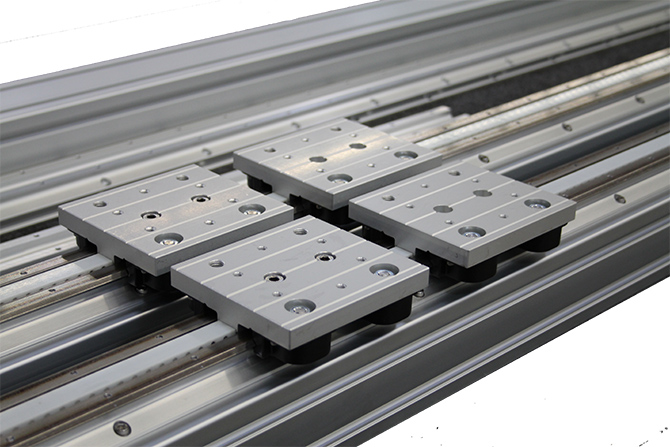
For industrial applications, most belt sprockets are made of either cast or ductile iron. That said, steel excels in designs that run at speeds exceeding those safe for iron pulleys — to 20,000 fpm. Likewise, aluminum pulleys run at high speed and have low inertia to boot. Another lightweight option is non-metallic pulleys — common in lawn equipment and power tools that transmit little torque and have relatively short design life. Other synchronous-sprocket options include specialty tooth profiles for better positioning accuracy or custom hub mounts and flanges.
Application example: Tight pulley connection helps robotics profile brain function
Now, BKIN Technologies sells machines that let neuroscientists and clinician scientists make scientific investigations into neurological conditions. The company’s KINARM is a robotic exoskeleton that moves with a patient’s arm to detect anomalies. When interacting with the robotic system, a patient either sits in a chair with robot arms affixed (in the case of a KINARM Exoskeleton Lab) or grasps two robotic manipulandums (in the case of a KINARM End-Point Lab). Then the setups run augmented reality software that creates virtual environments in which patients either direct hands to targets or interact with objects.
The robotic exoskeleton has a slotless motor that powers and drives the robot through a belt-and-pulley mechanism. The connection between motor and master pulley is critical, requiring zero backlash and no slippage. Early KINARM Labs used a pulley that attached to the motor shaft using set screws, but constant changing of motor direction during operation subjected this connection to high shock loads … loosening the screws and allowing backlash, shaft damage, and system failure. Now BKIN uses a more reliable connection called the Concentric Maxi Torque bushing system from Custom Machine and Tool Co. (CMT). The bushing offers zero backlash and high clamping torques. A low profile allows for direct coupling to the motor shaft — eliminating the need for a custom-length shaft and bellows coupler on the motor. The result of the mechanical shrink fit is ease of positioning and elimination of shaft damage.
In fact, CMT sells the pulley and bushing as an assembly. A mechanical shrink fit takes the form of a setscrew axial to the shaft that forces the tapered bushing into the hub’s matching taper. As the lever forces the two tapers together, the bushing slot compresses to clamp the pulley to the shaft. That same set screw can come off and go in the opposite hole to release the shrink fit and allow for removal or repositioning.
Leave a Reply
You must be logged in to post a comment.