Motion controllers range from single-axis smarts to programmable automation controllers (PACs) that synchronize hundreds of axes and plant data communications. These precision command centers are central to today’s motion-system innovation.

Consider how last year, the Composite Material Laboratory at Inholland University in the Netherlands installed a Moog Portable Test Controller for analysis of composite materials. The 100-kN hydraulic bench quickly tests lightweight materials for all sorts of products — including everything from aerospace and car parts to consumer sports equipment such as hockey sticks. The Moog test system includes hydraulic actuator, load frame, and controller.
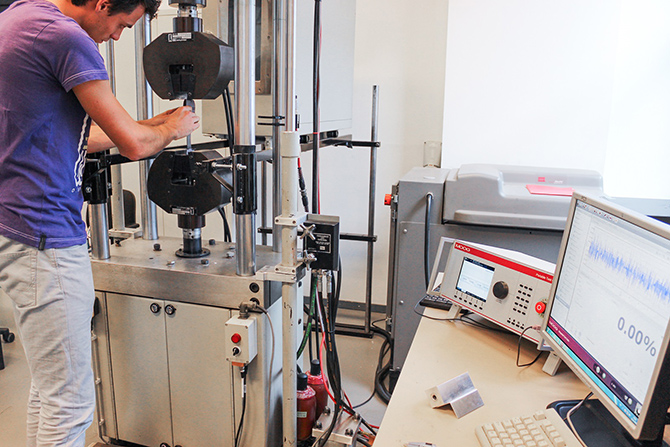
The lab recently did full-scale testing on bio-composite scooter parts to simulate road profiles. It’s also verified the ruggedness of cargo straps for aviation to show compliance with EASE regulations.
Software running on the controller gives engineers many options, so they can adjust the applied force during testing sequences. Integrated Test Suite software is versatile, and the Moog test controller uses an EtherCAT fieldbus interface for connecting slave devices needing time synchronization. A Gantner Instruments Q.bloxx measurement system links to the test controller for a modular measurement setup to connect to the test controller over EtherCAT.
Other motion controllers use advanced function blocks to improve specific applications
Consider how in some semiconductor-inspection machines, vibration-suppression function blocks can effectively shorten examination time. An X-Y stage moves a chip-carrying pallet so that a vision sensor can check chips one by one. After each pallet move, residual vibration persists — but the vision sensors can’t inspect chips until that vibration stops. Here, Sysmac Vibration Suppression library functions, a new addition to Sysmac Studio’s integrated development environment, from Omron Automation (running on the company’s NJ/NX controller) can trim settling time by two-thirds — for inspection cycles up to 100% faster than setups with no such suppression.
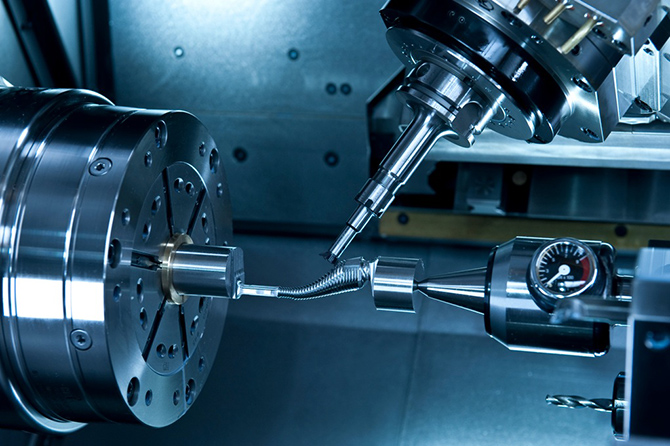
More specifically, Omron’s VSMoveParam1 calculates the S-curve parameters (including velocity, acceleration, and jerk) for suppressing vibration during single-axis positioning. The programming then uses this data to suppress vibration at system resonant frequency through corrective oscillations via the servomotor driving the axis in question. That boost maximum axis travel speed and (in many cases) workpiece quality or overall throughput.
In contrast, the VSConstVelProfile1 function in Omron’s Sysmac Vibration Suppression library calculates a position profile with a specified velocity in constant-velocity zones. Then it calculates a smooth position profile for each stretch of acceleration and deceleration so as to reduce residual vibration at stops … and suppress vibration during constant-velocity strokes. This particular function is useful when an application involves the handling of fragile items or liquids that can slosh or spill.

Controls in medical-implant manufacture
Medical-implant manufacturers must document and validate their products, and now CNC-controlled machines to produce prosthetics are making that easier. German manufacturer implantcast Corp. uses a CNC controller for transfer of CAD/CAM data to the actual production … including (among many other products) artificial titanium hip implants. The latter are mostly made through removal of material from stock.
Production of hip implants runs on DMG turning-milling centers with a Siemens CNC Sinumerik 840D sl. The machine also makes tailored instruments for the implantation surgery (including surgical rasps to prepare the bone). Fast data processing of the 840D sl helps in bulk manufacture of standard implants as well as custom patient- implants cut precisely to the associated bone structure with the help of a MRI or CT images. A Sinumerik Operate user interface integrates simple swivel commands that simplify setup. (Swivel functions are for swiveling a machine axis and an axis of the workpiece coordinate system.) The CNC also handles coordinate transformations.
Leave a Reply
You must be logged in to post a comment.