Edited by Mary C. Gannon, Senior Editor
Higher precision and robustness allow keyless shaft locking devices to meet the needs of today’s challenging applications.
When it comes to keyless shaft locking devices, the latest designs bring better solutions for today’s most advanced motion systems. Custom bushings, such as ETP designs from Zero-Max, lock onto a shaft to hold a drive component in place such as a gear, pulley, sprocket, roller, timing cam and similar devices. They are more precise and robust in what they do compared to designs like keys and keyways.
Enhanced shaft locking devices
While the keyless shaft locking devices of today function on a design principal that has been around for many years, refinement of this design concept—together with innovative variations—delivers exacting solutions for the challenging applications in which they are used. From a full range of models and sizes for most industry applications, a system designer can select the right keyless locking device that will greatly improve performance of a system’s design. One example is Zero-Max’s ETP bushings.

The primary goal of a motion system is to repeat a specific step or sequence of moves many times without deviation. Mounted components must be positioned and secured to ensure repeatability. Accuracy over many machine cycles becomes the challenge. So the device selected to position motion components, such as gears and pulleys, is critical to successful operation.
Unwanted material stress is often introduced into a system that uses traditional mounting methods such as keyways, setscrews and tapered shafts. When intermittent and reversing motion is required in a system, performance will worsen over time.

An option to prevent these forces is an ETP keyless bushing. These shaft-locking devices produce accurate and concentric mounting because of their unique design. ETP bushings incorporate a double walled sleeve encapsulating a pressure medium. When the actuation screw(s) is tightened, it forces the inner and outer walls of the bushing to expand uniformly against the shaft and hub of the mounted component. The result is an assembly that is concentric and also fast and easy to assemble. Another important design feature of these mounting devices is that they suit applications with repeated mounting and dismantling of components.
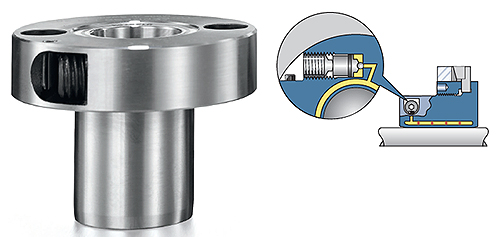
Benefits of bushings
The uniform locking pressure of these keyless connections in one of its specialized models makes a difference in preventing the types of problems often associated with other devices. They eliminate backlash, position misalignment, slippage and shaft play. They also produce uniform locking pressure enabling the keyless locking device to transmit higher torque and shock loads more consistently than one that relies on a key to transmit torque.
Besides preventing excess shaft wear, ETP shaft locking bushings address applications for synchronizing moving parts. They enable precise mounting of shaft components where frequent readjustments are needed, particularly where balance and runout are problems, and where common fastening, adjusting and holding of shaft components are required.

Immobility also matters. Test probes in gauging systems rely on positioning accuracy. To hold and locate the probe in an automated system requires precise, uniform locking pressure. A bushing design like that of the ETP product line enables a system designer to choose the exact model and size for the application.
Meeting the needs of washdown
Keys, keyways and other locking devices not only impose balance forces on a shaft, they add areas for debris to accumulate. In addition to posing maintenance problems, many locking devices often are bulky and heavy.
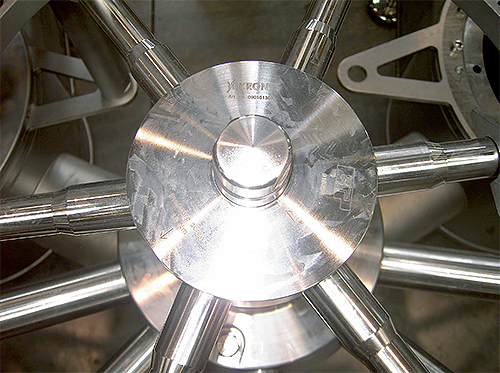
By comparison, the ETP Express stainless-steel models have sealed, clean lines that resist debris collection and clean easily without special maintenance. They suit systems requiring frequent washdown because they won’t corrode. They handle torque ranges from 34 to 6,400 ft-lb, and with this high torque capacity, suit locking into position gears, pulleys, sprockets and other components designed into food processing, packaging, pharmaceutical and medical systems.
Accurate positioning and synchronization
The ETP clamping concept operates effectively in large systems as it does in smaller systems. As an example, forming steel into different size bar stock requires positioning and fastening a system’s roll-forming wheels with accuracy so they stay in alignment throughout the process. A robust hub-shaft connection is required for this application. The ETP Hyloc model provides it in a difficult operating environment with excellent concentricity, despite high torque and radial loading.

Roll-forming wheels are centered, synchronized and locked into position using ETP Hyloc bushings. A rigid connection is made between the roll-forming wheels and shafts. The roll-forming wheel connection produces the required smooth and consistent bar stock. Easily adjustable, the Hyloc can be quickly repositioned on the shaft or removed for changing to another roll-forming wheel size. This minimizes system downtime.
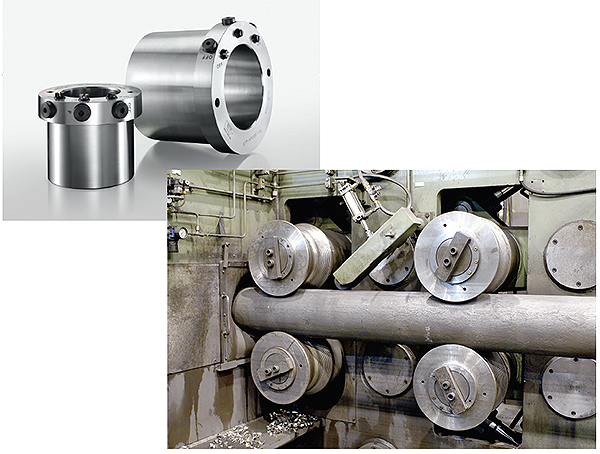
This ETP Hyloc model requires pressurization using a hydraulic pump that expands the ETP sleeve uniformly providing the robust connection to the shaft. With mounting pressure to 1,000 bar, this provides excellent concentricity to the mounted components. Also, the ETP Hyloc can be reset at different positions on the shaft without losing concentricity. Transmittable torque can be varied by altering the mounting pressure to accommodate heavy-duty systems such as large, automated pipe bending equipment.
Precise, high-volume designs
Industries with high-volume production requirements, such as food and beverage container manufacturing, benefit from another modified ETP knife holder bushing. Narrow in design, a series of these bushings is positioned between the system’s circular cutting blades. When located and tightened, the bushing’s double-walled sleeve expands uniformly against the shaft, creating a rigid friction grip on the shaft and the knife blade. Each bushing positions the circular knife securely for slitting thin steel sheet that is fabricated into beverage and food cans.
With concentricity of 0.006 mm, and a tested and proven service life for mounting and dismantling cutting blades thousands of times, this ETP design saves space along the shaft. With just one radial locking screw, mounting/dismantling is fast and accurate with no axial movement when mounting. These knife holder bushings are available on a custom basis to handle shaft dimensions from 50 to 200 mm.
Another design variation is the ETP-Unigrip axial tensioner that clamps work pieces and tooling firmly against a shoulder on a shaft. Using the same basic ETP clamping principal, this bushing incorporates, not just one, but two separate hydraulic clamping functions into the bushing body. It clamps down on the shaft and against the shaft shoulder. The single radial tightening screw actuates three internal pistons generating an axial force of 20 kN against the components being clamped. This design is available in standard sizes for 35 to 65 mm shafts.
Make informed decisions
Shaft locking devices make an important contribution to a system’s overall operating performance and success. From the many designs now available, choosing the right one for the application will ensure lasting results. System designers, especially engineers with new and unusual applications, should look at all available options when facing a design project. Protecting a high-value system from inefficient operation is important and problems can be avoided with an informed design.
Zero-Max
www.zero-max.com
Leave a Reply
You must be logged in to post a comment.