Advanced controllers can help streamline laser processing, allowing for tight synchronization of the laser and positioning stages, and helping meet the demand for higher precision in PCB manufacturing.
Warren Harvard • Country Manager, UK
Scott Jordan • Head of Photonics
Physik Instrumente (PI)
Modern electronic devices, from smartphones and laptops to kitchen appliances and wearables, are built upon printed circuit boards (PCBs). They are essential components that provide the physical structure and electrical connections necessary for the device to function properly. However, growing demand and increasing complexity in a continually expanding range of applications have presented new challenges for manufacturers. Miniscule features within intricate systems demand even higher levels of precision, and market demands call for enhanced throughput. Precision motion systems to control lasers have played a pivotal role in addressing these challenges and are propelling the advancement of PCB production, especially in processes like stencil manufacturing and laser direct imaging (LDI).
The electronics market’s need for more compact and powerful devices has resulted in smaller and smaller components, posing a significant challenge to the manufacturing of PCBs, where the reduction in size requires even greater precision in assembly and soldering processes. Stencil manufacturing and LDI have both proven helpful in addressing this and offer practical and effective alternatives for achieving high precision, fast production cycles, and enhanced flexibility in production pipelines.
PCB stencil manufacturing and LDI
The first of these approaches is PCB stencils, which are typically made from stainless steel and have laser-cut openings to precisely regulate the amount of solder paste applied to the pads. With the advent of miniaturization, these openings have shrunk in size, making it crucial to employ mechanical systems to cut them with even tighter synchronization of motion and laser control. At the same time, ‘multi-level’ stencils are often necessary, bringing another layer of complexity where the conventional X-Y planes are no longer sufficient, and an additional Z-plane is needed to create voids for optimizing solder paste control or addressing coplanarity issues. Gantry motion systems used to manufacture stencils must now offer two or three linear degrees of freedom – either X-Y or X-Y-Z configurations – while also providing the necessary extended travel distances and high speed.
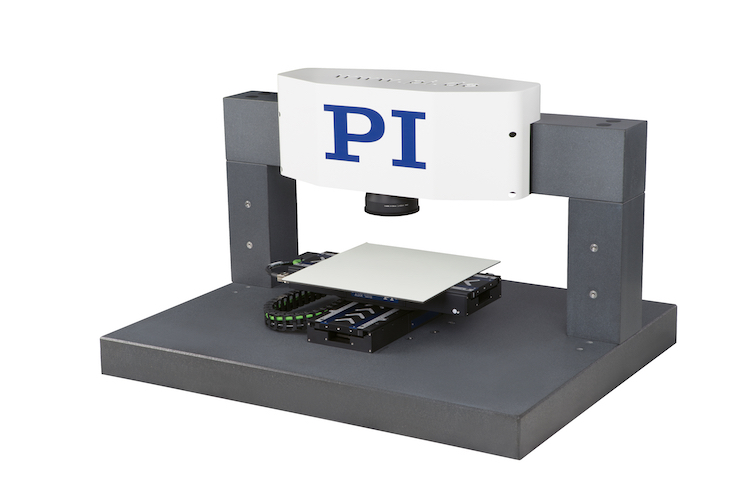
The alternative method of LDI has become an increasingly common technique for PCB fabrication, thanks to its exceptional precision and its ability to create small feature sizes essential for modern electronics. Instead of relying on traditional imaging processes with photo tools that can introduce distortion or degradation, LDI employs lasers to directly construct circuits on the board. Nevertheless, this approach demands high precision across the X-Y plane to maintain straightness and minimize yaw errors. Linear motors are a good option for this purpose, as they can offer excellent velocity control while scanning. Air bearing stages are also a common choice, exhibiting superior yaw performance, while optimized mechanical bearing stages provide high stability.
Laser processing
Both manufacturing of PCB stencils and LDI rely on accurate high-throughput laser processing, which requires motion systems capable of exceptional levels of control to be coupled to fast, reliable automation networks. The most recent iterations of these systems provide unparalleled flexibility to finely adjust manufacturing processes, enabling simultaneous control of servo-based stages and galvanometer scanners (galvos) without the user needing to be a laser or automation expert. These systems offer broad fields of view (FOV), eliminate stitching errors and use smart controllers to streamline the motion and hence the production process itself.
The first of these factors, a broad FOV, is important for PCB manufacturers because it allows inspection and processing on large portions of a PCB at once, which helps to increase efficiency and productivity. This can be particularly useful when dealing with larger or more complex PCB designs. There’s also the option to combine galvos with servo-based stages to create an extended field of view (EFOV) if necessary, increasing the area that can be accessed by the laser even further. However, these systems have different principles and requirements which means the control of a galvo is typically separate from that of the corresponding motion stage. As a result, the two platforms often operate in a step-wise manner, commonly referred to as ‘step and scan’, whereby the stage moves the scribing surface to the center of the galvo’s FOV, and control transfers from the motion system to the galvo. The main drawback of this start-and-stop approach is that it’s inherently inefficient, limiting throughput. But it can also lead to visible breaks or stitching errors at junctions where scanning must be conducted in two separate steps.

Introducing a feedback loop would, in principle, allow the scanner to detect and compensate for stage movement errors like this. However, this creates a delay between the scanner detecting and correcting errors, which will still lead to inaccuracies, particularly in applications requiring high-speed motion, such as a few meters per second or more. These errors can be in the region of 25 microns, which can be significant for applications involving laser processing of small features. Naturally, there has been growing interest in overcoming issues associated with stitching errors, and this has led to the development of control systems that combine high speed laser galvos and larger motion platforms into a single controller interface. These systems offer unparalleled flexibility in laser machining by effectively overlaying the small FOV of the scanner with the longer travel distance of the stage, providing seamless, continuous scanning. This approach also increases performance – particularly regarding precision path errors – and has a great impact on the throughput.
Smart controllers
Even when using the best motion systems, errors might still emerge when mechanical acceleration limits are exceeded, but slowing down the process is often not a feasible solution. Advanced motion controllers – such as the ACS-based A-824 and G-900 models equipped with smart software and EtherCAT connectivity from PI – have overcome this challenge by incorporating ‘look ahead’ intelligence. This feature automatically reduces laser speed in areas where errors may exceed specifications, particularly in instances of sharp cornering. Another strategy for optimizing corner quality is ‘sky writing’, a technique that eliminates abrupt changes in velocity or sudden stops, reducing processing time and minimizing errors. The ability to fine-tune laser power, adjust pulse placement, and even turn the laser on and off as needed is crucial. Linking laser power or, more relevantly, laser pulse output directly to the motion path velocity allows optimization of the laser cut quality. Achieving this level of control requires seamless communication between the motion controller and the laser source, something that ACS’ Laser Control Module readily accomplishes. These technologies let manufacturers meet the growing demand for PCBs and comply with ever more stringent design specifications with exceptional precision, while significantly increasing quality and throughput.
Physik Instrumente (PI)
www.pi-usa.us/en/
Leave a Reply
You must be logged in to post a comment.