Design engineers and equipment operators often view shock absorbers and isolators as nonessential fixit elements to add to original equipment only if it shows vibration or shock problems. Here we debunk this and other common misconceptions.
By Christopher Kudla, Product Manager | ITT Enidine
Engineering design is always evolving. With its progress comes a need to revolutionize the way plant managers and product engineers think of shock absorption and vibration isolation. That’s because all industries are demanding faster production or higher performance.
In most manufacturing (including that in industrial, food and beverage, and biopharmaceutical markets) demand for efficiency means running machines more often and at faster speeds. Complicating matters in food and beverage and biopharmaceutical designs is concurrent increase in regulation. Confounding designs in industries such as oil and gas is rapid innovation that’s completely changed (in just a few years) the machinery of choice. Here, minimizing shock and vibration from the start makes for longer-lasting designs. More after the jump.
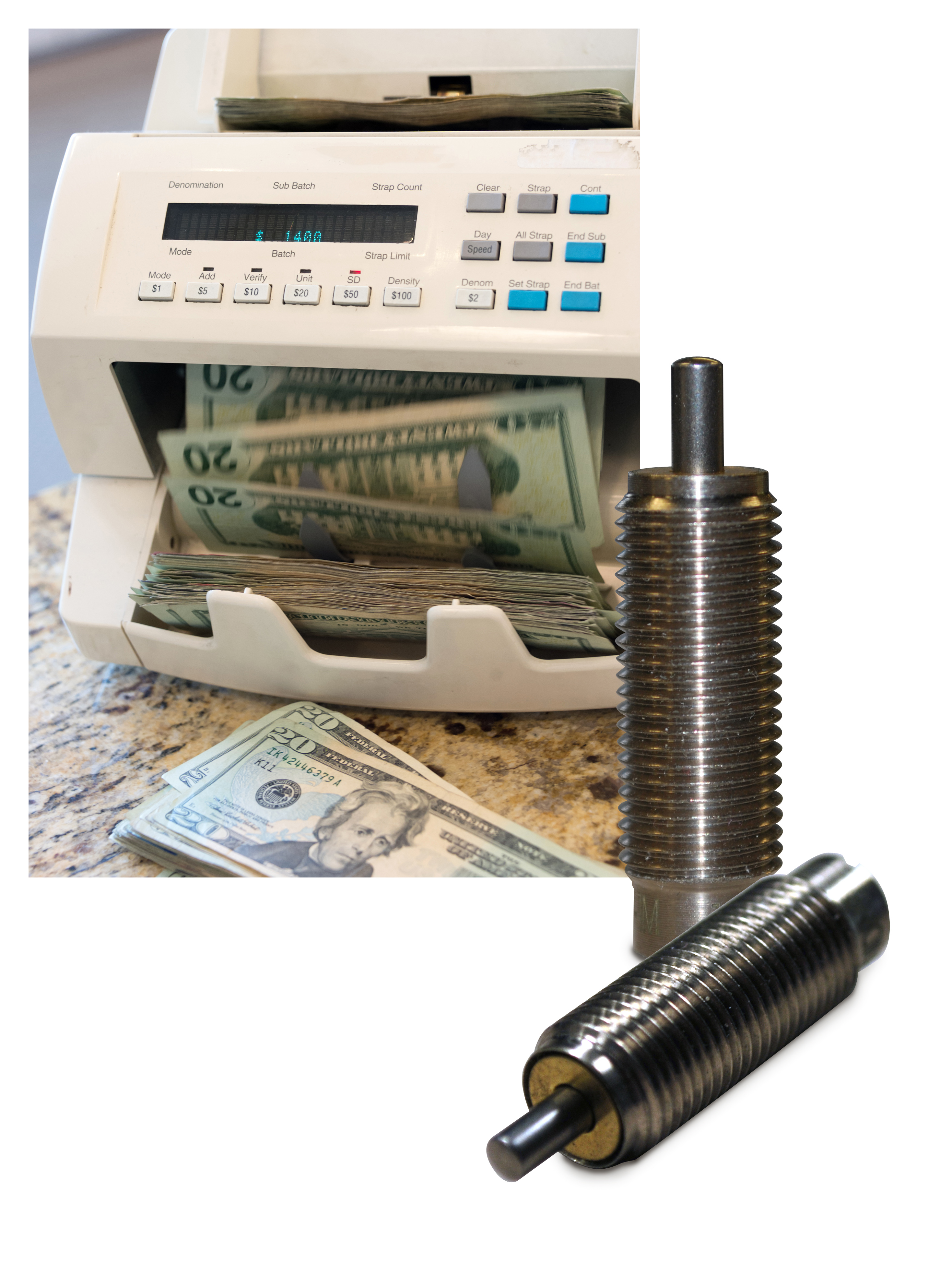
Modern engineering is also incorporating more sensing and processing technology into all aspects of design. This shift calls for mitigation tuned specifically to applications and prevention of vibration and shock in even the smallest parts of machinery — as in a sensor on a piece of agricultural equipment, or on military vehicles subject to harsh impact landings, for example.
Basics of vibration mitigation
In industrial applications, shock and vibration is everywhere. It degrades overall safety, efficiency, and machine output. Many times, equipment operators react to shock and vibration problems by seeking and integrating products to mitigate shock and vibration only after issues arise. However, proactively designing mitigation into equipment boosts long-term machine health and reduces total cost of ownership by preventing failures.
To review, shock is impact that occurs at the end of a movement, and it can take place anywhere there’s a hard stop or collision. For example, in automated designs, that might be in a warehouse storage and retrieval system, in doors that open and close, or on a facility’s conveyor. In contrast, vibration is small, high-speed oscillations caused by frequency excitation through some inherent imbalance. Vibration occurs in rotating or reciprocating equipment (electric motors, pumps, compressors, engines and gearboxes, for example) and often fatigues components and mounting points. The primary goal when handling shock and vibration is to reduce acceleration to which the equipment or design is subject.
Industrial shock absorbers are mechanical devices that bring a moving object in industrial machinery (such as a conveyer system or crane) to rest. They provide controlled deceleration by converting kinetic energy into thermal energy. This thermal energy then safely dissipates into the atmosphere to prevent additional equipment shock and damage. Other commonly used shock absorbers include rubber bumpers or springs and cylinders. However, these often exhibit undesirable recoiling and different forms of shock loading and vibration.
Vibration isolators reduce the effects of shock and vibration. A major problem in industry is how vibration causes damage to internal machine components and electronics. Here, wire rope isolators, air springs, and elastomers are some solutions. One caveat: Elastomeric products attenuate noise and vibration levels, while wire rope isolators do this and also provide shock attenuation capability.
Damping misconceptions versus reality
Needing shock absorption is not sign of bad engineering. As mentioned, a common misconception is that shock absorption is no more than a Band-Aid solution to address fundamental design flaws. The logic is that if a piece of equipment or manufacturing process needs a shock absorber to boost uptime, then it was improperly designed or is malfunctioning.
In fact, nearly all industrial equipment experiences some level of shock during operation. By incorporating shock absorption into equipment or facility upfront, engineers can get higher equipment operating speeds with lower reaction forces on structures, equipment, and products.
What’s more, integrating shock-absorption technology reduces impact forces, which often lets designers choose smaller, cheaper, and more efficient design structures. Lower forces mean less maintenance and downtime because equipment is subject to less overall wear and tear. More specifically, reduction of acceleration g reduces force where:
Force = Equipment weight x Number of gs
Reduced impact forces means less stress on structural members. So lower stress lets engineers use smaller parts or build designs with less support structure while still maintaining a given amount of strength and performance.
In addition, incorporating shock absorption into the design lets it run at higher velocities in production processes while eliminating concern about end-of-motion impact . In other words, shock-absorption products manage kinetic energy at the very ends of machine-axis movements — so moves can happen as fast as possible without slamming, banging, bouncing or breaking afterwards. This boosts production speeds and throughput from the start, for shock absorbing that’s better tailored than what’s installed after machine failure. Plus high-velocity applications with shock absorbers don’t need to slow down before the end of motion and there will not be any bounce when the movement stops. This also means an increase in production speeds since the time spent moving the product or material is done as quickly as possible and without threat of failure.

In addition to higher throughput, proactively adding shock absorbers to equipment can improve product quality since there are lower accelerations (number of gs) during movement. When molds and dies are cushioned upon closing, overall production quality sees improvements as well. Without any residual energy remaining when the mold closes there will not be any bounce or rebound which can cause molding defects.
Ultimately, building shock absorption technology into original equipment and facility design means that equipment can handle higher forces more quickly and with smoother motion.
Approaches to vibration isolation
As with vibration mitigation, vibration isolation can also be misconstrued as an afterthought, rather than a proactive solution. Operators generally believe that if equipment needs to be isolated with flexible mounts it is because the equipment is worn out, bearings are old or something is out of balance.
Facility personnel can’t entirely prevent vibration in equipment but can be proactive in reducing it by building vibration isolation into original designs. It’s expensive to keep equipment perfectly balanced and maintain tight tolerances. It’s also inefficient to add structural braces and patches as a way to prevent damage to the surrounding structure. In contrast, adding vibration isolation such as wire rope isolators or air springs is cost effective and efficient. Designing equipment and processes upfront with vibration isolation reduces forces to save machinery structures from fatigue on brackets and welds. With less equipment wear and tear comes more efficient structure design without the threat of broken parts and downtime.

In addition, reciprocating equipment such as pumps and compressors with higher levels of vibration can be used in the manufacturing process without damage to bolts or adding heavy and inefficient structural braces. Adding vibration isolation can reduce this risk and boost pump and compressor performance.
Proactive mitigation also improves operator safety with better ergonomics. With less vibration, operators are able to handle equipment more productively and with greater ease of use.
Reducing vibration in equipment and facilities with built-in isolation solutions lets components vibrate by controlled design and not at random.
Application examples for shock and vibration mitigation
Cameras on remote operated vehicles often face issues with excessive vibration. These devices are typically not designed with isolators, but as the performance of today’s compact cameras continues to increase, vibration from surroundings is increasingly evident in output video. Getting smooth video and images necessitates incorporation of isolators. Due to the size of these cameras, it’s challenging to get the right fit and meet requirements with retrofit isolators. But OEMs who incorporate compact wire rope isolators into original designs get great design performance for this high-end market.
Bank–note counting machines use vibration isolation to prevent bounce in moving components as each note is counted. Any bounce disrupts the precise movement of the machine and causes counting errors or jamming. Financial applications have zero tolerance for error. When one OEM designed shock-absorption technology into one such counting machine, it realized increased speed and efficiency without risk of inaccuracies.
Leave a Reply
You must be logged in to post a comment.