A common function of a conveyer system is to accumulate products — in other words, to stop them from moving along the conveyor to create a buffer, establish a queue, or smooth out differences in material movement between upstream and downstream operations.
But traditional accumulation methods allow products to bump into each other and stack up as they stop, one-by-one, behind the lead product. This causes a build-up of pressure between products — referred to as backpressure — which can lead to product damage. And in traditional accumulation systems, the conveying media continues to run even when the products are stationary, creating unnecessary friction and wear and reducing efficiency.
The solution to these problems is a zero pressure accumulation conveyor.

Accumulation conveyors can use a variety of conveying media, including belts, chains, or rollers. Regardless of the conveying media, zero pressure accumulation is achieved by establishing individual product zones. For belt and chain conveyors, each zone is driven by its own 24 VDC motor and monitored by a photoelectric sensor. (Note that these individual DC motors replace the traditional setup of a single AC motor that controls an entire conveyor section.)
As each product moves along the conveyor, the controller uses feedback from the photosensor in the product’s current zone to determine whether the zone ahead is occupied or not. If the next zone is occupied, the controller stops the product from moving until it the zone ahead is free.

Image credit: Glide-Line
Roller conveyors that use motorized rollers can also achieve zero pressure accumulation by incorporating individual zones driven by a 24 VDC motors. However, roller conveyors that use belt- or chain-driven rollers operate a bit differently. Like other designs, the conveyor is divided into zones. But in these designs, when the photoelectric sensor in one zone detects that the zone ahead is occupied, the belt or chain is pneumatically lowered away from the rollers, stopping movement in that zone.
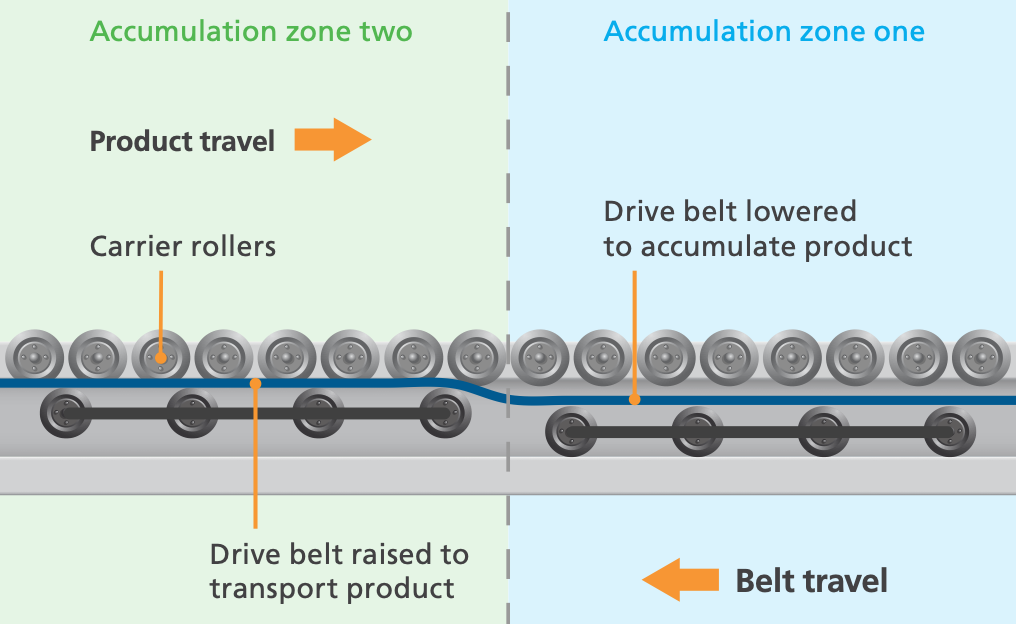
Image credit: Honeywell Intelligrated
Each zone in a zero pressure accumulation conveyor has a predefined length suitable for one product, pallet, tote, or carton, although some models — particularly those with rollers as the conveying media — allow zone lengths to vary along the conveyor to accommodate products of different sizes. And some designs allow for zone lengths and configurations to be reprogrammed, providing the flexibility to accommodate larger or smaller products without significant changes to the conveyor itself.
Zero pressure accumulation is especially useful for preventing damage when the product being conveyed is very fragile or when large and small (or light and heavy) products are interspersed along the conveyor. It also significantly improves the efficiency of the conveying system, since the conveying medium is stopped when product isn’t flowing, and reduces wear-and-tear by eliminating the friction that results when rollers, belts, or chains continue to operate under stationary products.
Leave a Reply
You must be logged in to post a comment.