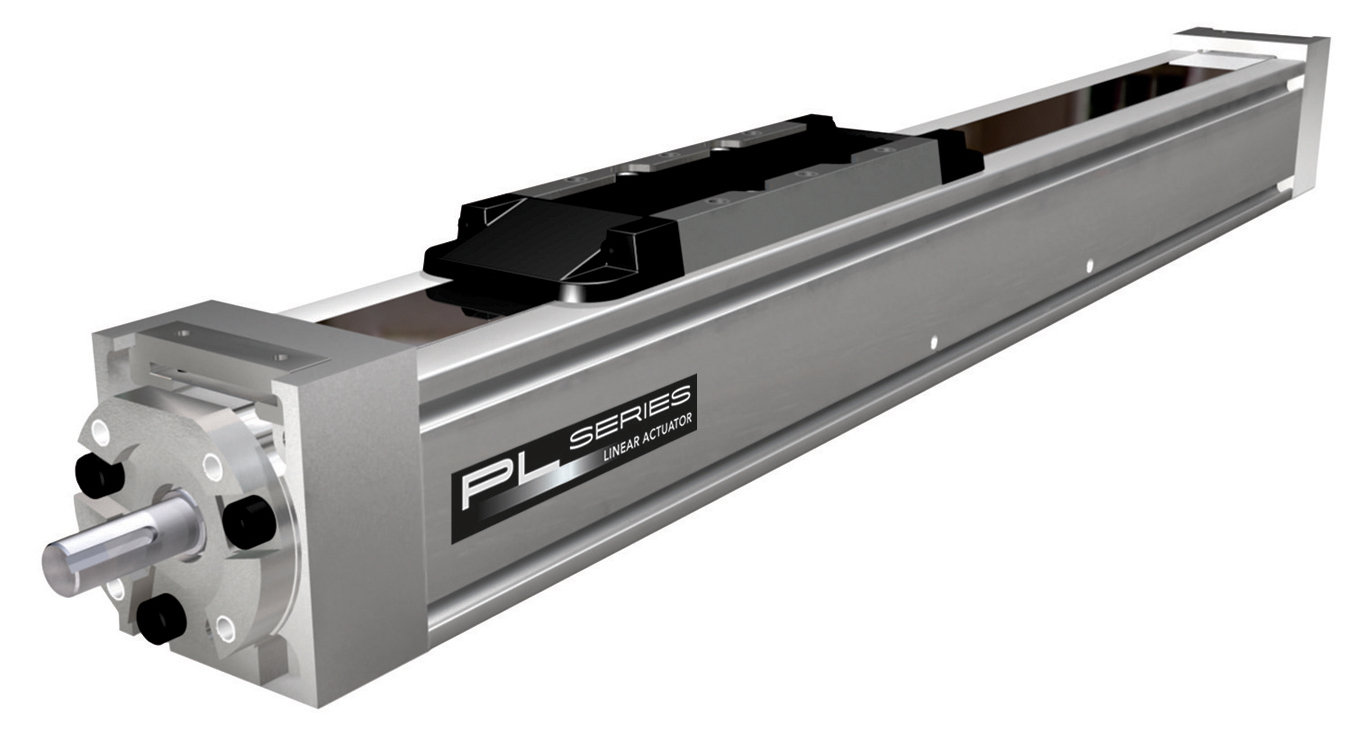
Updated May 2015. || Ballscrews are used to change the direction of motion—from either rotational motion to linear motion or linear to rotational. The advantage of ballscrews is that they accomplish this function with minimal friction.
The basic components of a ballscrew are a nut, a screw with helical grooves, and balls (often made from steel, ceramic or hard plastic material) that roll between the nut, the screw and the grooves when either the screw or nut rotates. Balls are routed into a ball return system of the nut and travel in a continuous path to the ball nut’s opposite end. Seals are often used on either side of the nut to prevent debris from compromising smooth motion.
Over the last few years, advances in manufacturing and materials have improved ballscrew performance so machine designers today can get better linear motion with them at lower cost. Some improvements include the fact that the latest generation of ballscrews has more load density than ever, giving designers higher capacity from a smaller package. There is also a trend toward more miniaturization, but also faster ballscrews with rolled and ground screw manufacturing methods.
Ballscrews suit applications needing light, smooth motion, applications requiring precise positioning, and when heavy loads must be moved. Examples include machine tools, assembly devices, X-Y motion, Z motion and robots.
Ballscrews are usually classified according to factors such as lead accuracy, axial play and preload, and life/load relationship. Lead accuracy refers to the degree to which the shaft’s rotational movements are translated into linear movement. With lead accuracy and axial play determined by the manufacturing method of the ballscrew shaft and the assembly of the nut, high lead accuracy and zero axial play is generally associated with relatively higher-cost, precision ground ballscrews, while lower lead accuracy and some axial play is associated with lower-cost, rolled ballscrews. Fabricated by rolling or other means, ballscrew shafts yield a less precise, but mechanically efficient and less expensive ballscrew.
Axial play is the degree to which a ball nut can be moved in the screw axis direction without any rotation of either nut or screw.
Preload is applied to eliminate axial play. It removes backlash and increases stiffness.
Ball recirculation inside the ball nut can affect precision and repeatability. Thus, ball nuts are available with a range of preload options to reduce or remove the axial play as they rotate around the screw. Minimal axial play allows better accuracy, for example, because no motion is lost from the clearance in the balls as they reengage.
There are several techniques for preloading. Some common methods include oversizing the balls inside the nut housing; using the so-called “double-nut” or “tension nut” method; or using a manufactured offset in the raceway spiral to change the angle of ball engagement (the “lead shift” method) and deliberately force the balls into a preload condition. Each method has its advantages and disadvantages, but all serve to minimize or eliminate backlash between the nut and screw.
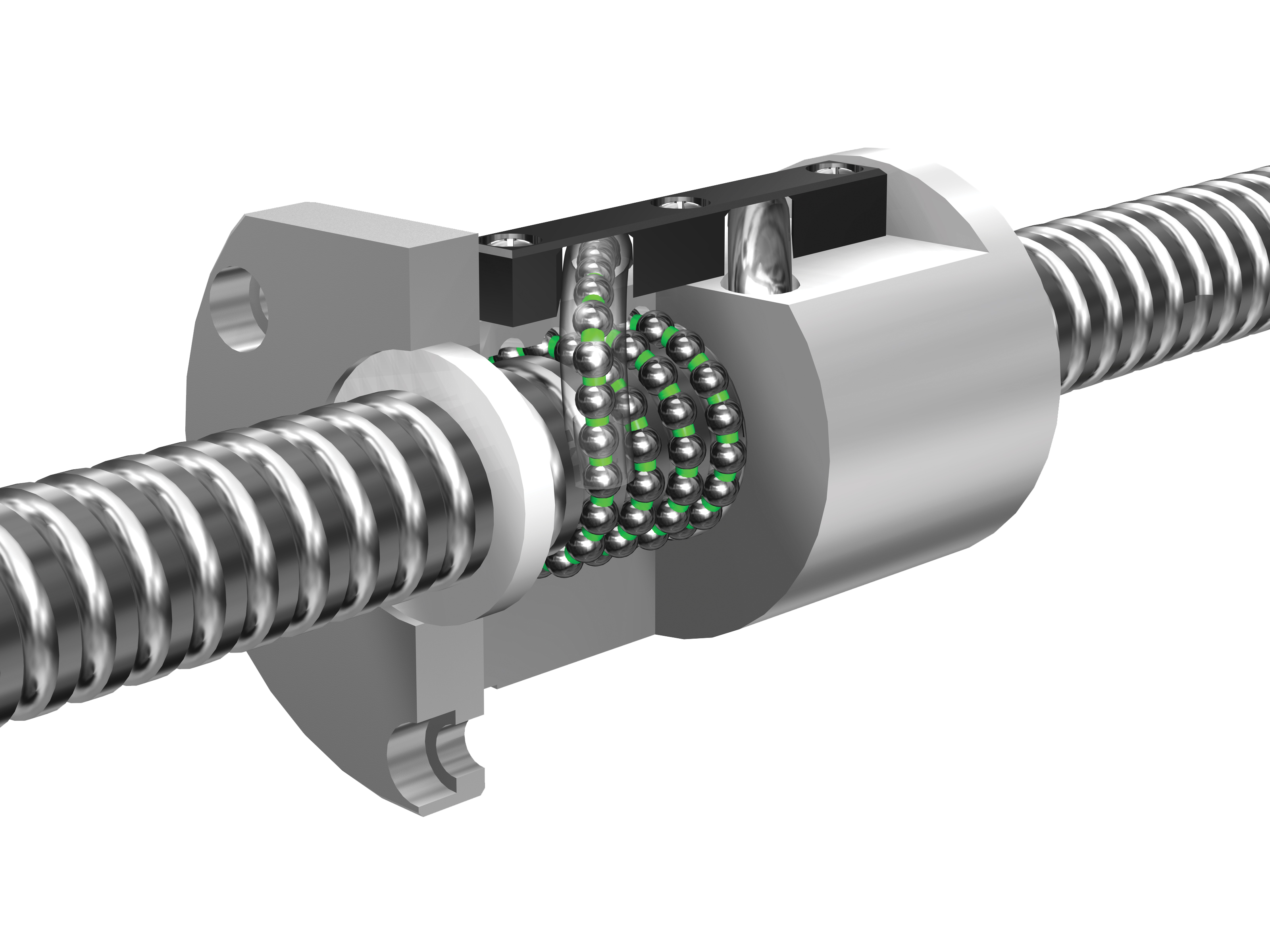
Perhaps the biggest overall benefit of a ballscrew is that it has high efficiencies that can be well over 90%. By contrast, Acme leadscrews average about 50% efficiency or less. There are also minimum thermal effects. Backlash can be eliminated through preloading. Ballscrews also offer smooth movement over the full travel range. The higher cost of ballscrews can be offset by decreased power requirements for similar net performance.
One drawback to ball screws is that they require high levels of lubrication. Ballscrews should always be properly lubricated, with the correct type of lubricant, to prevent corrosion, reduce friction, extend operating life and ensure efficient operation.
Because ballscrews are a bearing system, they’ll need some type of lubrication to avoid metal-to-metal contact of the balls in the raceway. While the lubrication choice can be either oil or grease, it’s advisable to avoid solid additives (such as graphite) as they will clog the recirculation system. An NLGI no. 2 type grease is recommended, but it should also depend on the application, whether food-grade or another special type of lubrication is required. Ballscrews, especially those used in machine tools, generally require lubricants with EP additives to prevent excessive wear.
For more information on ballscrew-driven actuators, also visit our sister site:
linearmotiontips.com/category/linear-actuators
Also read the related article: How to Size and Select Ballscrews: An Engineer’s Guide
The lube amount will be fixed, but the frequency of lubrication will vary depending on factors such as the move cycle characteristics or contamination in the environment. Contaminated lubrication can increase friction. In addition, ballscrews can fail if the balls travel over metal chips or dirt in the ball thread raceway. Using lubricants recommended by machine tool manufacturers can help prevent this effect. Using telescopic covers or bellows can help keep ballscrews clean when used in environments with many contaminants.
Proper installation of ballscrews is also important … but care must be taken, as ballscrews are more prone to damage during installation than leadscrews.
Leave a Reply
You must be logged in to post a comment.