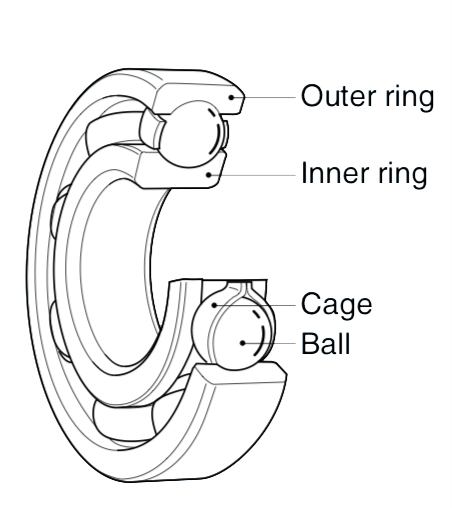
Image credit: NTN Corporation
Rotary bearings are common components in motion systems. They’re used in gearboxes, motors, pulleys, fans, pumps—virtually any time a shaft is rotating, rotary bearings are there to reduce friction and support radial or axial loads.
The classification of rotary bearings begins with the type of bearing that supports the load—ball or roller. Within the ball and roller types, the next distinguishing feature is the primary load direction that the bearing can withstand—radial or axial (aka thrust). Then, ball bearings are further classified by the configuration of the outer ring, while roller bearings are further categorized by the shape of the rollers.
While there are dozens of variations of rotary bearings—including designs made for specific environments, mounting configurations, and applications—the most common categories are covered here.
Rotary Bearings

Ball Bearings—Radial

Image credit: SKF
Within the ball bearing family, deep groove ball bearings are the simplest type, with raceways that nearly match, or conform, to the diameter of the balls. This type is suitable for radial loads and for axial loads in either direction, although their load capacity is relatively small compared to other bearing types. For higher load capacity in a relatively small footprint, deep groove ball bearings are commonly available in a double-row design, with two rows of balls instead of one.
Angular contact ball bearings are designed so that the line that connects the points of contact of the inner ring, ball, and outer ring runs at an angle radially to the bearing. The contact angle increases load capacity, but it means the bearing can withstand an axial load only in one direction, so these bearings are typically used in pairs or in a double-row design (essentially two angular contact bearings mounted back-to-back) in order to withstand axial loads in both directions.
Four-point contact ball bearings are single angular contact bearings that are designed to withstand high axial loads in both directions. They can also withstand combined axial and radial loads, as long as the axial component is predominant.
Ball Bearings—Thrust
Thrust ball bearings are made of two relatively thin bearing rings (sometimes referred to as bearing plates or washers), with raceways designed to take axial loads, in either one direction or both directions. Radial loads are typically not permissible for thrust bearings, and speed capabilities are limited (as low as 20 to 30 percent of their radial bearing counterparts in some cases).
Roller Bearings—Radial
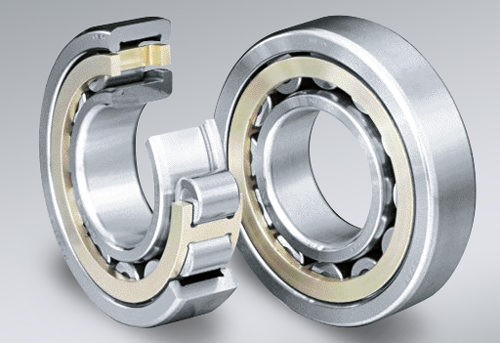
Image credit: NSK Ltd.
With rollers supporting the load, roller bearings have higher load capacities and higher rigidity than ball bearings of similar sizes. The type of load they can support depends primarily on the shape of the roller.
Cylindrical roller bearings can withstand high radial loads, while double-row cylindrical versions having extremely high radial load capacity and high rigidity in the radial direction. Although standard cylindrical roller bearings are not capable of taking axial loads, some designs include internal ribs or collars that allow them to handle relatively small axial loads in one or both directions.
Needle roller bearings use long, thin rollers, with a length that is anywhere between three and ten times the diameter. They have good radial load capacity, but the primary benefit of the needle design is that it has a thin cross-section, for applications where high radial capacity is required but space is limited.
Unlike cylindrical and needle roller bearings, tapered roller bearings, which use conical rollers to support the load, can withstand axial loads in one direction. Tapered roller bearings can be thought of as the roller version of the angular contact ball bearing, and like their ball bearing counterparts, tapered roller bearings are often used in pairs or in a double-row design, to counteract axial forces that are produced in the bearing when a radial load is applied. The tapered design also improves rolling properties and reduces friction within the bearing.
Spherical roller bearings use barrel-shaped rollers and have two inner raceways inclined at an angle to the bearing axis, and one spherical-shaped outer raceway. This gives them a self-alignment capability, very high radial load capacities, and the ability to withstand axial loads in both directions.
Roller Bearings—Thrust

Thrust versions of roller bearings generally follow the strengths of their radial counterparts, but with thrust (axial) load capabilities.
Cylindrical thrust roller bearings can accommodate high axial loads and are able to withstand impact loads, although radial loads are not permissible.
Similarly, needle thrust roller bearings can withstand high axial loads, but in a much smaller form factor due to the use of needle bearings.
Tapered thrust roller bearings can be single-direction or double-direction type, indicating whether they can accommodate axial loads in one direction or in both directions. Like their radial counterparts, tapered thrust roller bearings have “pure” rolling motion, which means less heat generation and less wear.
Spherical thrust roller bearings can take very high axial loads and small to moderate radial loads, with the ability to withstand some misalignment.
For more information on rotary bearings, visit our sister site: bearingtips.com.
Leave a Reply
You must be logged in to post a comment.