Typically mounted deep inside an assembly of moving parts, industrial springs often go unnoticed, despite their importance to motion control and industrial equipment. In fact, they’re found in everything from door closing mechanisms on machine tools to mechanical seals in rotary unions. While springs are readily available in custom designs and variations, there are three primary types used in industrial applications: compression springs, extension springs, and torsion springs.
Compression springs
Springs that resist axial compressive forces are categorized as compression springs. They’re one of the most common types of springs and one of the most efficient at storing energy. When force is applied to a compression spring, it compresses, or shortens, and stores energy. As the spring tries to return to its original length, it releases this energy and “pushes back” against the load.

Image credit: Zimmer Group
Wave springs are a type of compression spring made of flat wire with waves added to each turn of the wire. The addition of waves in the spring results in a high spring force with a lower working height than traditional round-wire compression springs. Industrial applications for wave springs include vibration isolators and bearing retention for rotating equipment.
Extension springs
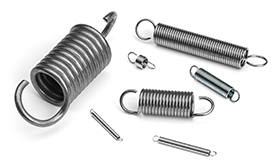
Image credit: Lee Spring
Springs that resist tensile forces — forces that attempt to pull them apart — are known as extension springs or tension springs. Extension springs are coiled with an initial tension, and when the spring is lengthened, it creates a “pulling” force as it tries to return to its original shape. These springs have loops or hooks on the ends so they can be easily attached to components that need to be held together via the spring’s force.
One way to describe the primary difference between compression and extension springs is their load at zero deflection. Compression springs have zero load at zero deflection. Extension springs, on the other hand, experience a load at zero deflection due to their initial tension. A common example of extension springs are those used on trampolines. Industrial uses include medical devices and door mechanisms on automated equipment.
Unlike a compression spring, which can only be compressed to its solid height, an extension spring has no mechanism to prevent overloading.
Torsion springs
Torsion springs are designed for applications that need resistance to twisting forces (torque), rather than axial tension or compression forces. Torsion springs are helically wound springs with arms on the ends that rotate about the spring’s central axis. The arms are connected to the external components, which apply a load to the spring. It’s important to note that the load on a torsion spring should only be applied in the direction that causes the spring’s diameter to decrease. A common example of torsion springs are those used in clothespins.
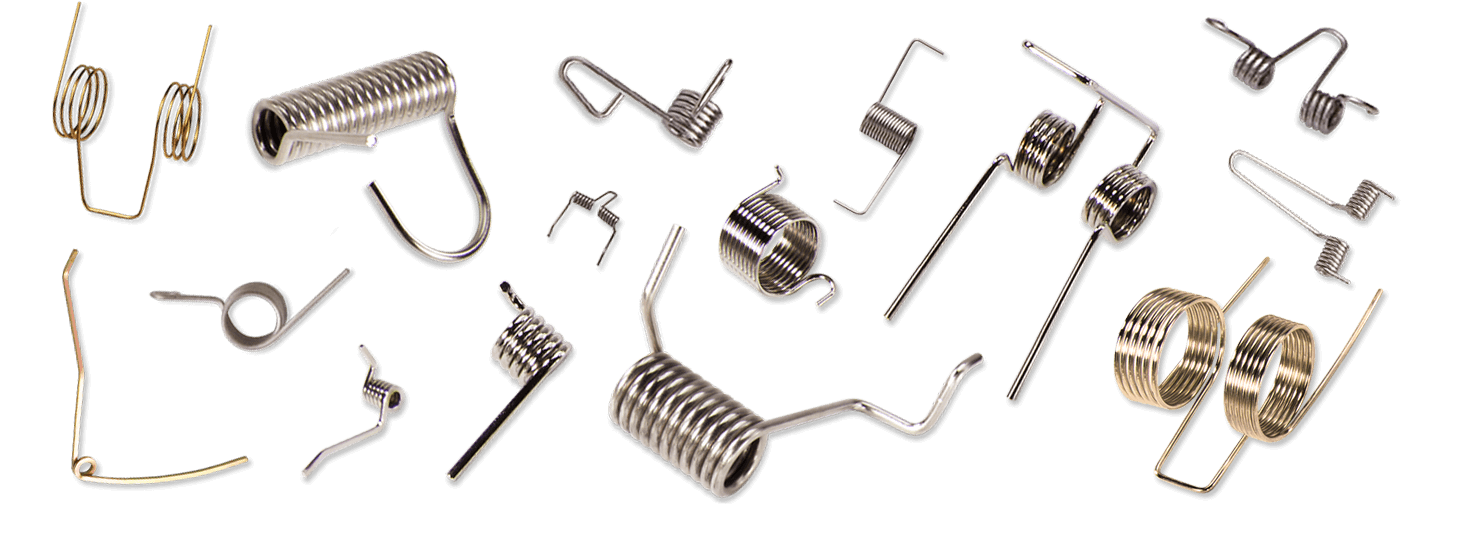
Image credit: Newcomb Spring Corp.
For applications that require very high torque, two torsion springs can be combined, with a space between them, to create what is known as a double torsion spring.
Feature image credit: Lee Spring
Leave a Reply
You must be logged in to post a comment.